Situation
A steel pipe mill had been outsourcing a hard surfacing (cladding) application for one of their highest use wear parts, an hourglass shaped steel roller. The customer needed to lower their costs, and explore savings opportunities by bringing the process in-house, to avoid expensive and cumbersome outsourcing and transportation costs.
Problem
In order to effectively take this job in-house, the solution required the following:
- Sub Arc Welding (SAW): High deposition rates and cycle time speed was critical for this job in order for it to yield significant cost savings. The rollers are large, and require deposition of 20-25 lbs per hour deposition in order to make this process profitable.
- Hydraulic Tilt Function: In order to apply SAW, the welding head requires an optimal vertical angle, and due to the gradual angle change of the hourglass shape of the roller face, they require a positioner that can quickly and accurately reposition the workpiece to keep up with the subarc's high deposition rate and avoid process bottlenecking.
- Size Variability: Since these rollers are used in all pipe fabrication diameters up to 84”, the rollers vary in size. The solution would require an easy switch over for part size variability.
Solution
LJ responded with a subarc cladding system that fit the customer's needs and cut one of their top 5 largest outsourcing expenses by introducing the LJ pipe cladding positioner, integrated with a Column and Boom Welding Manipulator with a Lincoln AC/DC-1000 Subarc system, to their pipe fabrication facility.
Here's how the new process works:
Step 1: Load the workpiece on the adjustable spindle, on the custom cladding welding positioner.
*Please note, for internal LJ testing, we used a cylinder as we did not have access to the customer’s proprietary workpiece. Actual workpiece is similar in hourglass shape to the image below:
Step 2: Position SAW welding head in position, then hit “Weld Start”.
Since the positioner rotation speed is controlled by the integrated column and boom welding manipulator, the rotation is always rotating at the correct speed.
- Place SAW head in position
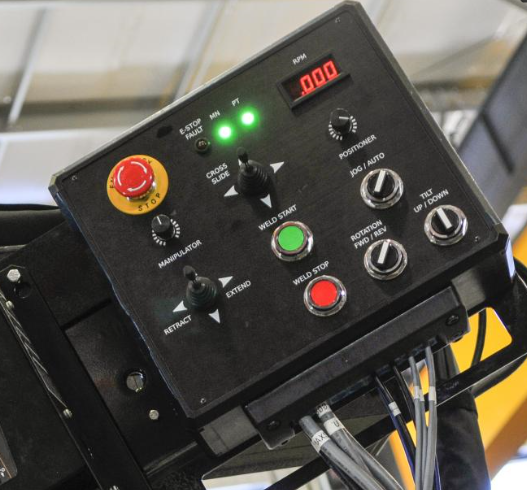
- Hit “Weld Start”
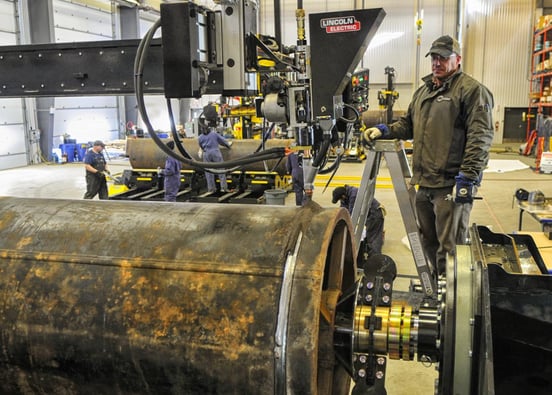
- Operator watches the weld as the positioner rotates workpiece (Flux recovery/delivery, welding camera, and seam tracking available)
Step 3: Once a pass is completed, the custom welding positioner is tilted to place the welding head in optimal position, then Step 2 is repeated.
Step 4: Once the roller the entire surface of the roller is completed, it is removed, and sent for grinding to reface the surface.
CONCLUSION:
Initially, the end user was unsure of the ROI of investing in a new process that they had outsourced for years. LJ designed a simple and effective system to achieve all of their needs, delivering on the required cost savings, and with minimal training time for their new “in-house” process. Through the use of innovative material handling and welding integration, the customer was able to achieve over 20lbs/hour deposition, with the possibility of applying twin wire applications in the future to further increase this already impressive deposition rate. Additional automation features such as automatic indexing, seam tracking and remote view cameras, could be included to further maximize efficiency in the future.
After the first order of this cladding system the customer realized such a large cost savings that they ordered a duplicate system.
- Do you have an expensive process that you currently outsource?
- Do you want to improve a current process that you are spending too many man-hours on?
Topics: Productivity, Submerged Arc Welding, Research & Development