Situation
A manufacturer of emission control systems for mobile and stationary internal combustion engines had been experiencing rework issues and required a more consistent process for welding silencers, catalytic converters and other large cylindrical-shaped emission controls components.
The customer's main facilities are located in Toronto, Ontario, Canada and they had previously implemented semi-automated column and boom welding manipulator systems with excellent results. With an expansion into the Texas, USA market, the company came to LJ for another system - including full material handling - to build on their previous successes that included faster cycle times, higher quality welding, and drastically reduced rework.
Old Process
All the equipment was previously fabricated using manual MIG welding processes, along with conventional rollers, cranes, labor-intensive methods for lining up the sections during welding and fit up. This left room for error and rework costs were jeopordizing the facilities long-term profitability and competitive edge.
The LJ Solution
Within four months, LJ consulted, process-audited, delivered and commissioned a fully automated welding cell that included the following:
- MNP-600 Welding Manipulator: Open arc Lincoln S350 running GMAW process mounted to compact LJ column and boom manipulator.
- Horizontal Oscillator: used to oscillate the welding head and simulate the "weaving"motion required for a quality MIG weld.
- Electronic Height Actuator: utilizing voltage feedback system to continually adjust torch height, and maintain a consistent torch-to-work distance for optimum welding performance .
- Welding Manipulator Track Drive: for indexing from seam to seam quickly and safely.
- Material Handling/Rotators: Specialized Version of 10 TMR Double Jointing System for quick and simple fit up of the vessel (silencer component) sections.
Turnkey system: included tank turning rolls, track drive systems, CaB manipulator and welding package, fully integrated.
Integrated Controls: system start/stop, welding and vessel rotators controlled from the column and boom manipulator HMI or remote pendant.
Operator's Platform for ease of control and visibility when welding.
Key Results
- Customer was able to reduce cycle times and increase throughput, because welding speeds were increased by approximately 25% over manual welding speeds, and on-arc time was greatly increased with no stopping during weld sequences.
- Customer was able to refit their shop on a tight budget and within their required timeline.
- Inevitable safety hazards were mitigated with the new handling and welding environment.
- Rework issues were virtually eliminated; savings realized would quickly pay for the system.
Have a question about your application or would like the spec sheet for this system?
Topics: Case Studies, Boom and Column Welding Manipulators, Productivity, Research & Development
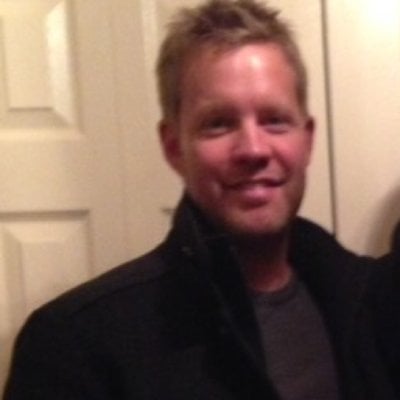