Situation
A large structural steel fabrication company was in need of equipment to help increase welding deposition rates for crane bridge beams and structural steel girders.
The customer previously utilized cumbersome manual welding systems with low output and varying quality. These processes also demanded a higher level of skill and precision, and thus made the fabrication process much more expensive. The customer was interested in upgrading to an automated submerged arc welding (SAW) system that would offer much higher through-put, consistent weld quality and vastly improved worker safety.
The customer was clear that a gantry-style welding system would be necessary to secure a competitive edge. After evaluating the available options, the customer chose to partner with LJ because of the following considerations:
- Deposition Rates- first and foremost, the customer wanted the highest possible welding deposition rate for the best possible price.
- Automation- there was a requirement for a fully automated welding process, utilizing the latest seam tracking, camera, and joystick + touch screen technology, with a single HMI interface
- Quality and durability- LJ has a reputation in the industry for building exceptionally heavy duty, best in class equipment, which is a must for metal fabrication facilities where thousands of tons of heavy steel are processed.
- Customization- LJ has developed a reputation within the industry of tailoring equipment to best suit each customer, which in turn ensures our customers get maximum value out of every LJ system.
- Training and Technical Support- the customer valued LJ's in-house engineering expertise, as well as submerged arc welding specialists on staff who are able to help train each customer to not only use and maintain the equipment, but to get the absolute maximum performance out of the equipment.
Background: The Old Process
The customer previously utilized cumbersome welding bugs (subarc tractors) combined with GMAW metal-cored wire, which were inefficient, slow and variable quality. Overall deposition rates were 10 lbs/hr when welding due to lower deposition processes (single wire, one weld at a time) and lower arc-on time.
Expensive labor, bottlenecks in production, inconsistency in quality, and rework were all issues that had to be factored in with the old process, especially given that the local economy was in a downturn and competition was fierce. The customer had the foresight to know that an up-front investment in automating this welding, was crucial to their ongoing and future competitive edge.
The LJ Solution: A New Structural Beam Welding Gantry System
The free consultation resulted in the commissioning of the following beam welding gantry system specs:
- Dual-head Twin-Wire Miller DC-1000 submerged arc welding: Maximized overal deposition rates and minimized overal capital costs as the dual twin-wire welding systems (total of 4 wire welding) provided best ROI for customer. LJ's engineering and submerged arc specialists recommended process changes that allowed the customer to make optimal use of each 1,000Amp capacity power source. By maximizing amperage in the twin wire process to just under 400Amps per wire, deposition rates of 26lbs/hr per twin wire head were achieved, and because dual-heads were utilized, overall deposition rates were increased to a whopping 52lbs/hour equating to a 520% higher deposition rate compared with their original process.
- Pressured flux delivery/storage tank: efficient flux recovery, pressurized flux tank delivery systems, and 1,000lb wire spool drums, allowed customer to weld continuously for long periods of time between consumables refilling, which meant much less downtime and more arc-on time.
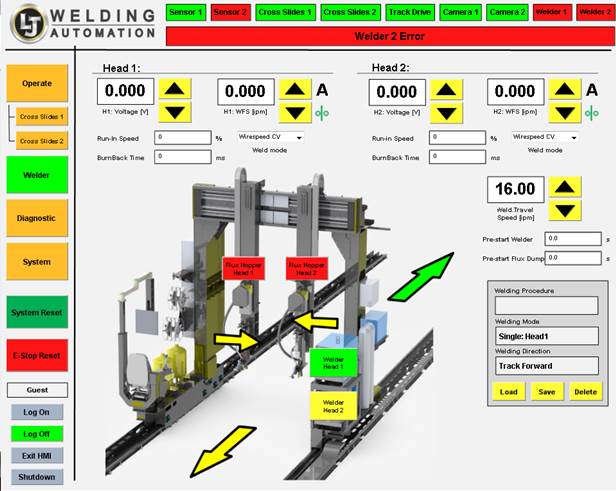
- Operator Interface: Operator chair designed to be on floor level, along with temperature activated hand control grips, HMI touchscreen, and console set up for maximum comfort and worker safety... LJ's engineers designed the system to be one that operators would want to use every day!
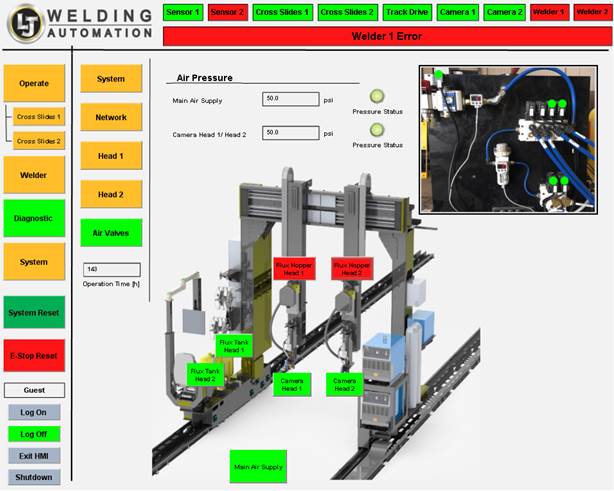
- Vision laser seam tracking - vision seam tracking was combined with large servo controlled 84" travel vertical and 12" horizontal cross slides to allow for large range of part sizes and flexibility during welding.
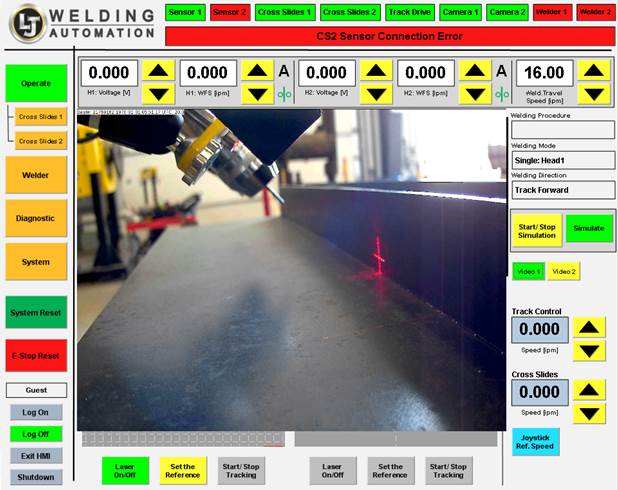
- Camera system: for viewing on screen so that operator could view both welds safely, up close, in real time from operator chair
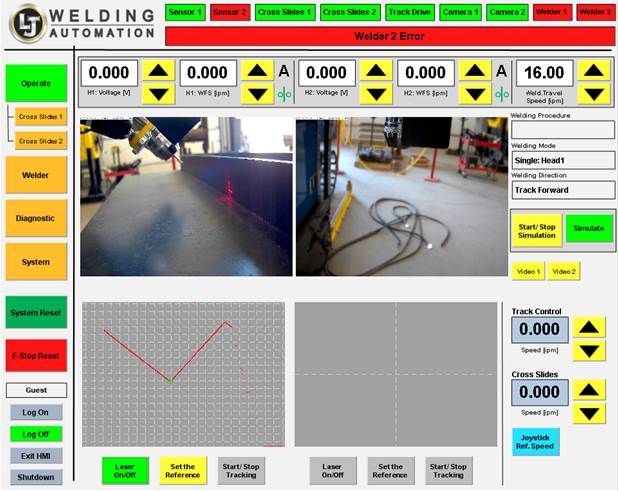
- Precision track drive: will allow for up to 100+ ft of uninterrupted, maximum productivity, high deposition welding.
Preliminary Results
- Deposition rates that can exceeding 52 lbs/hr of total metal deposition through the use of 2 welding heads and 4 wires allowed for up to 520% higher deposition rates than previous process!
- Uninterrupted, fully automated welding of very long structural components at high deposition rates = maximum productivity
- Far fewer consumables change over delays due to large flux delivery/recovery and welding drum systems
- Operators were able to sit in comfortable operator chair,close to floor, and have optimum position for viewing the work
Stay tuned to find out more with on-site interview with the customer now using this state of the art subarc structural beam welding gantry system.
Have a custom job you'd like free expert advice on?
Have a question? We'd like to hear from you!
Beam Welding Gantry Update
Below are some images of the new beam welding gantry:
Topics: Case Studies, Productivity, Submerged Arc Welding, New Products & Innovations, Research & Development
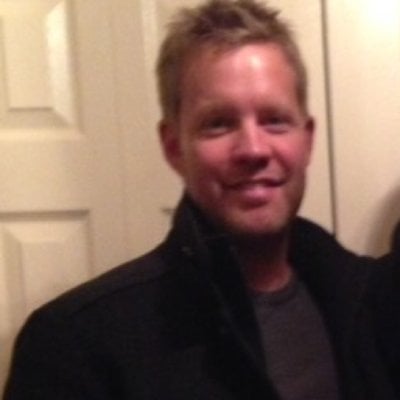