The demand for renewable energy is rapidly increasing, and with it, the need for efficient, reliable, and scalable solutions in wind tower fabrication has never been greater. As wind turbines grow in size and complexity, fabricators face new challenges in handling large sections, ensuring precision fit-ups, and maintaining high productivity without compromising quality. This is where LJ Welding Automation’s 100 Ton Growing Line + Predictive Tandem Subarc System comes in—an innovative welding system designed to meet the rigorous demands of wind tower fabrication.
Challenges in Wind Tower Fabrication
Wind tower fabrication presents unique challenges due to the sheer size and complexity of the structures involved. Sections of towers can span over 100 feet in length, with diameters as large as 16 feet. Handling and aligning these massive sections requires not only strength but extreme precision. The quality of the welds is critical, as any imperfections could affect the structural integrity of the tower and, in turn, the safety and efficiency of the wind turbine.
Traditional fabrication methods, which often rely heavily on crane operations and manual adjustments, can be time-consuming and prone to errors. Fabricators need solutions that can automate and streamline processes while ensuring the highest levels of precision.
Growing Lines: Increasing Efficiency and Precision
LJ Welding’s Growing Lines are designed to streamline the fit-up, alignment, and assembly processes for large cylindrical components, offering a comprehensive solution to industries requiring high-capacity fabrication. These systems are particularly beneficial for the construction of wind towers, tanks, and pressure vessels, where precision, safety, and efficiency are paramount.
LJ's Growing Lines are capable of handling a wide range of loading capacities, accommodating large sections of up to 100 tons and diameters of up to 240 inches. These systems are engineered to reduce manual labor, minimize crane usage, and ensure precise alignment of components. By automating the fit-up process, fabricators can experience a decrease in alignment time by up to 65%, making them a critical component in large-scale fabrication projects.
The key benefits of LJ’s Growing Lines include enhanced operator safety, reduced material handling, and increased productivity. Their flexibility allows operators to adjust for varying diameters and lengths, making the systems adaptable for multiple applications across different industries. Whether for wind tower section fabrication, or other types of vessels, these systems ensure that components are aligned perfectly before welding, which improves weld quality and reduces rework.
One of the most significant advantages of using LJ’s Growing Lines is the reduction in cycle times and the increase in throughput. By automating key processes, LJ’s systems ensure that operations can be completed more quickly and with greater precision, all while maintaining high standards of safety and reliability.
At the core of this 100 Ton Growing Line + Predictive Tandem Subarc System is the 100 Ton Growing Line, which allows fabricators to handle and align wind tower sections with ease. The growing line supports sections up to 120 feet in length and 16 feet in diameter, making it ideal for the large-scale demands of wind tower construction. One of the key differentiators of this growing line is its steel eccentric wheels, which straddle the joint between tower sections, ensuring precise fit-up. These wheels, combined with hydraulic actuators that adjust for varying diameters, enable the system to accommodate towers with different outer diameters (OD) or circumferences, ensuring a perfect alignment every time.
By minimizing the need for crane usage, the growing line not only speeds up the alignment process but also reduces the overall operational cost and risk. The system’s mechanized ground systems are designed to handle these massive components safely and efficiently, distributing the load evenly with double rocker wheels. This provides greater stability and control during the fabrication process.
If you're looking to elevate your fabrication efficiency and precision, explore the growing lines we currently offer and discover how they can transform your operations. CLICK HERE
Predicitive Tandem Subarc System: Flawless, Predictive Results
LJ Welding Automation’s Predictive Tandem Subarc Welding System goes beyond just material handling—it ensures the welding process is as precise and efficient as the alignment. At the core of this advanced system are the Tandem Lincoln ACDC-1000 power sources, which offer real-time adaptability to variations in joint conditions. Whether dealing with slight imperfections in fit-up or changes in material, the system automatically adjusts its welding parameters to deliver flawless, high-quality results.
The Lincoln Power Wave® AC/DC 1000® SD integrates Waveform Control Technology®, allowing for precise control over both welding current and voltage. This technology optimizes arc stability, reducing common weld defects like porosity and cracking, and ensuring a smooth, high-quality finish, even under challenging conditions. With the ability to handle both AC and DC welding processes, the Power Wave system provides the versatility required for complex applications, such as wind tower fabrication and large-diameter pressure vessels.
An impressive feature of this system, utilizing the Tandem Lincoln ACDC-1000 power sources, is its high deposition rate, exceeding 65 lbs/hour, which makes it one of the most productive welding setups available. Combined with a 300-lb heated flux feed, the system allows for extended, uninterrupted operation, ensuring large-scale projects can be completed efficiently and with minimal downtime.
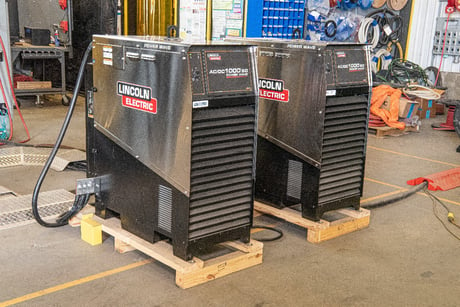
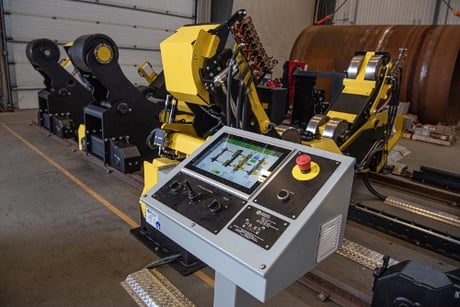
Central to the seamless operation of this system is LJ Welding’s PLC/HMI (Programmable Logic Controller with Human-Machine Interface). The PLC/HMI is a robust, touchscreen-enabled controller that gives fabricators real-time access to essential welding variables and full control over the welding process. Key parameters like deposition rate (lbs/hr) and heat input (kJ/inch) are displayed live on the interface, allowing operators to monitor and fine-tune the welding process as needed.
The PLC/HMI is fully integrated with the welding power source and offers a high degree of customization. Operators can select between different operating modes and secondary parameters such as pre-flow, run-in wire feed speed (WFS), and burn-back time. This level of control enables fabricators to optimize welding conditions for different materials and joint conditions, improving both weld quality and efficiency.
Additionally, the PLC/HMI enhances quality control (QC) by providing real-time data on essential welding variables, such as heat input and deposition rates, allowing for quick adjustments during the process. This real-time feedback loop ensures higher productivity, fewer defects, and more consistent results. The controller also allows operators to easily adjust the rotation direction and workpiece surface travel speeds on any LJ material handling system, further optimizing the handling and welding process.
In addition to the advanced power sources and controls, LJ’s system also incorporates a Subarc Column & Boom Welding Manipulator, designed to enhance precision and efficiency. LJ engineers these manipulators with a focus on boom stiffness, welding head stability, and ease of use. The nearly vibration-free boom provides a steady platform for the automatic welding head used for submerged arc welding (SAW), ensuring consistent, high-quality welds.
The manipulator features a powered column, which allows the boom and welding head to be positioned at the optimal height for large-scale workpieces like wind towers or industrial vessels. This ensures precise alignment and reduces the risk of weld defects caused by movement or misalignment.
The system’s design allows for easy operator control, integrating seamlessly with the PLC/HMI for centralized control and real-time adjustments. This setup gives operators the flexibility to adjust for varying workpiece sizes while maintaining high weld quality and consistency, ultimately boosting productivity and reducing downtime.
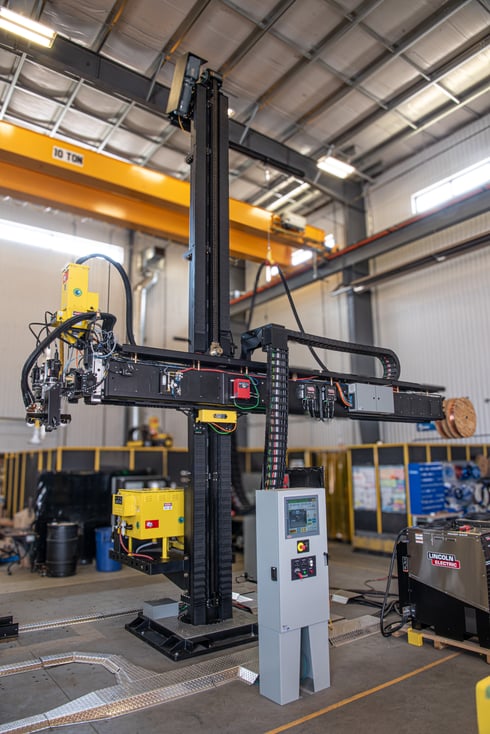
What sets this whole 100 Ton Growing Line + Predictive Tandem Subarc System apart is the balance it strikes between automation and manual control. While the system automates most of the heavy lifting—monitoring and adjusting weld parameters for optimal results—it also gives operators the flexibility to make manual adjustments when necessary. This is particularly valuable for large-scale projects where flexibility and precision are critical, such as in wind tower fabrication.
Safety, Reliability, and Scalability
While performance and precision are crucial, safety and reliability are equally important, especially when handling large and heavy components. The 100 Ton Growing Line is equipped with a range of built-in safety features, including AC brakes, limit switches, and safety catches. These mechanisms ensure that all operations are secure, reducing the risk of accidents and ensuring the safety of workers in the fabrication process. In industries where downtime can be costly and hazardous, these safety features are essential for maintaining smooth operations.
The system is also designed with scalability in mind, making it future-proof for the ever-growing wind turbine industry. As turbine sizes continue to increase, the 100 Ton Growing Line + Predictive Tandem Subarc System is ready to accommodate sections larger than 120 feet, making it adaptable to the industry’s future demands. This scalability ensures that the investment in this equipment pays off for years to come, as it can grow with the needs of fabricators and the renewable energy sector as a whole.
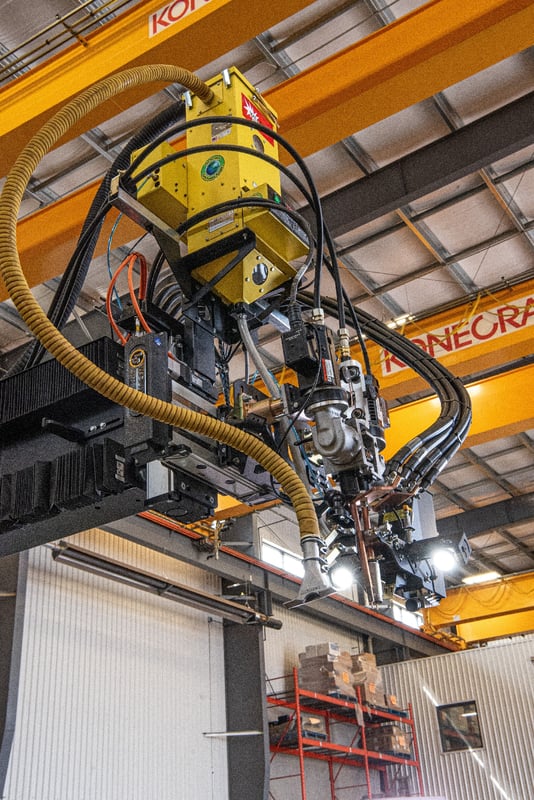
A Game-Changer for Wind Tower Fabricators
The combination of advanced material handling and adaptive welding technology makes LJ Welding Automation’s 100 Ton Growing Line + Predictive Tandem Subarc System a true game-changer for wind tower fabricators. This system addresses the key challenges of the industry—precision, speed, safety, and scalability—offering a solution that not only meets but exceeds industry standards.
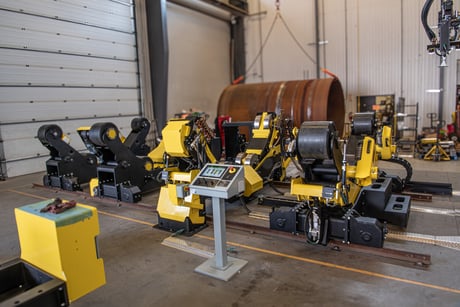
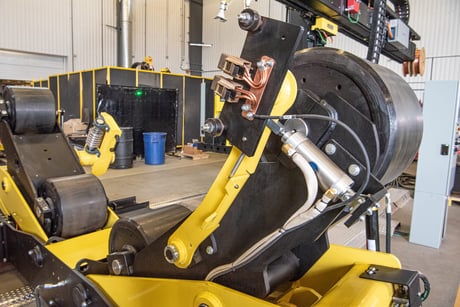
By reducing manual intervention, minimizing crane usage, and delivering adaptive, high-quality welds, this system allows fabricators to significantly boost their productivity while ensuring the highest quality standards. In a world where renewable energy is becoming increasingly important, having the right tools is essential to staying competitive. LJ Welding Automation’s growing line technology offers fabricators the ability to streamline their operations and tackle the future of wind tower fabrication head-on.
Ready to Elevate Your Wind Tower Fabrication? Get in Touch Today!
Topics: Case Studies, Productivity, New Products & Innovations